In the ever-evolving world of printing technology, businesses and creators constantly look for methods to achieve superior quality, cost-efficiency, and versatility. Among the options available, UV printing, DTF (Direct-to-Film) printing, and the hybrid UV DTF (Ultraviolet Direct-to-Film) printing have garnered significant attention. Understanding their unique features, strengths, and limitations is crucial to selecting the right solution for your needs.
This blog provides an in-depth analysis of these three technologies, complete with a comparative table to help you make informed decisions.
1. Overview of UV Printing
UV printing refers to a process where ultraviolet light is used to cure or dry ink, adhesives, or coatings as they are printed. This instant curing process allows UV printers to work on a wide variety of substrates, from paper and plastics to metals and glass.
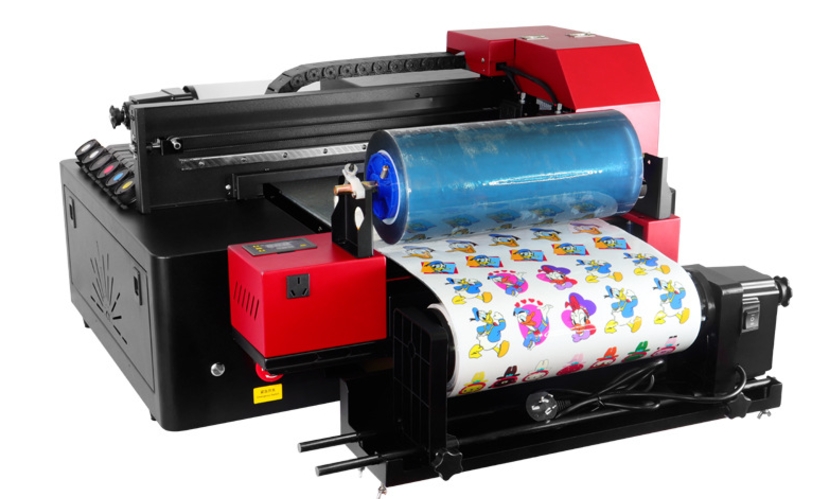
Key Features:
- Fast Curing: UV light instantly dries the ink, preventing smudging.
- Versatility: Works on rigid and flexible materials.
- Durability: UV prints are resistant to scratches, fading, and weather.
- Eco-Friendly: UV curing reduces emissions of volatile organic compounds (VOCs).
Applications:
- Signage and banners.
- Packaging and labels.
- Customized promotional items (e.g., phone cases, mugs).
Limitations: UV printing struggles with flexible surfaces and textiles as cured inks are rigid, leading to potential cracking or peeling.
2. Overview of DTF Printing
DTF printing, or Direct-to-Film printing, involves printing designs onto a specialized film that is later transferred to textiles using heat and adhesive powder. It has emerged as a game-changer for the apparel industry, providing an alternative to traditional screen printing and direct-to-garment (DTG) printing.
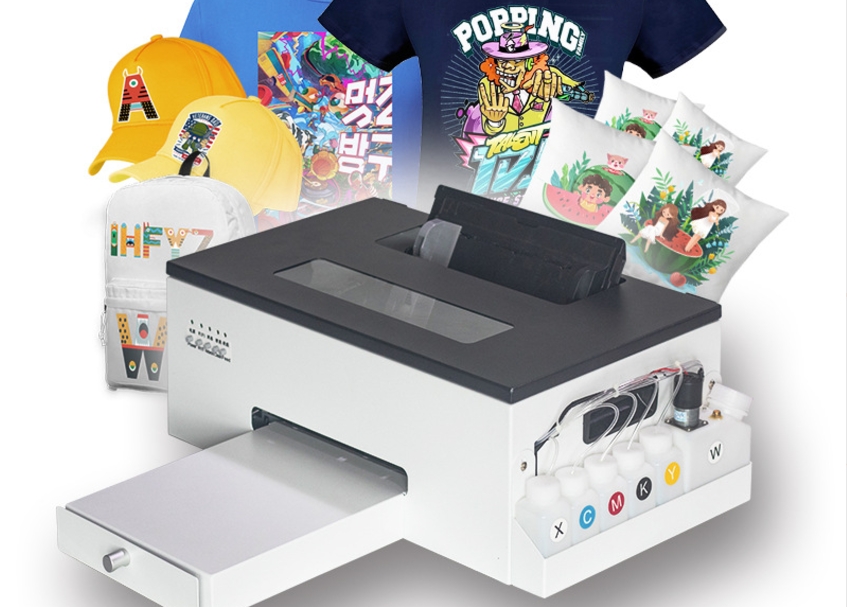
Key Features:
- Flexibility: Ideal for fabrics of all kinds, including cotton, polyester, and blends.
- Vibrancy: Produces bright, vivid designs with excellent detail.
- Scalability: Suitable for both small runs and mass production.
Applications:
- Custom t-shirts and hoodies.
- Bags, caps, and other fabric accessories.
- Team uniforms and promotional apparel.
Limitations: DTF is generally limited to textile applications and may lack the durability required for certain demanding environments.
3. Overview of UV DTF Printing
UV DTF printing is a hybrid innovation that combines UV printing's precision with DTF's versatility. This method prints designs onto a specialized transfer film using UV-curable inks. The design is then applied to non-textile surfaces like glass, metal, and ceramics using an adhesive layer.
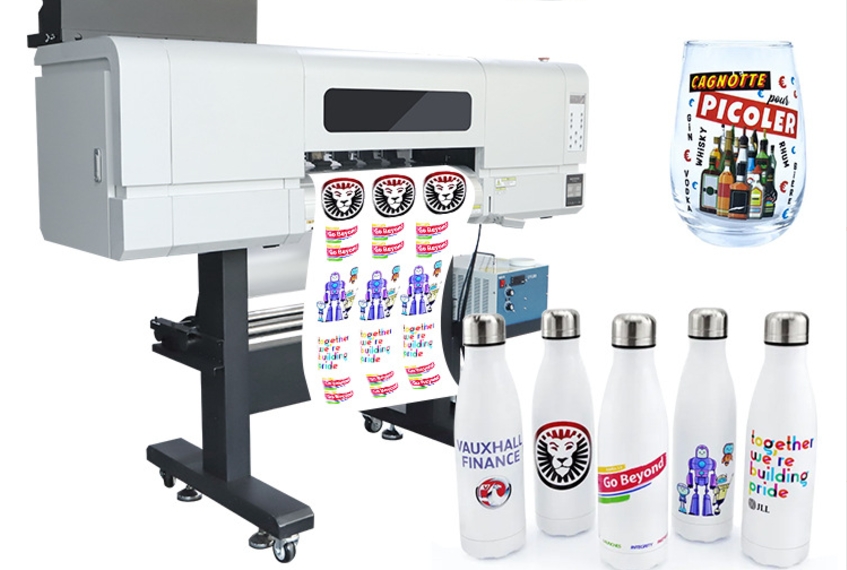
Key Features:
- Durability: Offers scratch-resistant, waterproof designs.
- Versatility: Compatible with various surfaces like plastic, glass, and wood.
- Ease of Use: Requires minimal surface preparation.
- Precision: Produces intricate, high-resolution designs.
Applications:
- Custom drinkware and bottles.
- Decorative plaques and tiles.
- Branded office supplies (e.g., pens, USB drives).
Limitations: UV DTF designs are rigid once cured, making them unsuitable for highly flexible or porous materials.
4.UV Printers vs. UV DTF Printers
Similarities:
- Technology: Both UV printers and UV DTF printers use UV heating technology and UV ink.
- Print Quality: Both produce high-resolution, durable, and vibrant prints.
Differences:
- Printing Process:
- UV Printers: Print directly onto the surface of the object. However, uneven or sloped surfaces may result in less satisfactory prints.
- UV DTF Printers: Print the design onto a PET film first, allowing the transfer of the design to various materials and surface types, making them more adaptable.
5.UV DTF Printers vs. DTF Printers
Similarities:
- Transfer Process: Both require printing designs onto PET film before transferring them to the desired object.
- Material Compatibility: Both can print on a range of materials using the film transfer method.
Differences:
- Ink Type:
- UV DTF Printers: Use UV ink, offering quick curing and vibrant colors.
- DTF Printers: Use specialized DTF ink, which is designed for heat-transfer applications.
- Transfer Method:
- UV DTF Printers: Involves laminating the film with a laminating machine, followed by pressing the film onto the object and peeling off the cover without requiring pre-heating.
- DTF Printers: Require pre-heating the film during the transfer process, which can be more time-consuming for large-scale operations.
6. Key Differences Between UV, DTF, and UV DTF Printing
The following table highlights the key distinctions among these technologies:
Feature | UV Printing | DTF Printing | UV DTF Printing |
Primary Application | Rigid and flexible surfaces | Textile printing | Non-textile surfaces |
Materials Supported | Paper, plastic, metal, glass | Cotton, polyester, blends | Glass, wood, metal, ceramics |
Ink Type | UV-curable inks | Textile-specific pigment inks | UV-curable inks |
Durability | High (scratch/weather-resistant) | Moderate (requires proper care) | High (scratch/water-resistant) |
Flexibility | Low | High | Low |
Ease of Transfer | Direct printing | Film transfer using heat | Film transfer using adhesive |
Production Speed | Fast | Moderate | Moderate |
Cost Efficiency | High for large volumes | Cost-effective for small runs | Medium-high |
Best For | Signage, promotional items | Apparel and accessories | Custom non-textile items |
7. When to Choose Each Technology
When to Choose UV Printing:
UV printing is ideal for projects requiring:
- High durability and weather resistance.
- Direct printing on rigid materials.
- High-speed production.
When to Choose DTF Printing:
DTF printing is best for:
- Custom apparel and textile-based products.
- Small to medium-sized production runs.
- Detailed, vibrant designs on fabrics.
When to Choose UV DTF Printing:
UV DTF printing excels in:
- Creating customized designs on non-textile surfaces.
- Producing scratch-resistant, detailed outputs.
- Low-volume, high-value projects such as gifts and corporate branding.
8. Practical Examples
Example 1: Retail Branding
A retailer wants to brand acrylic keychains and ceramic mugs.
- Solution: UV DTF printing ensures durable, vibrant designs that withstand daily use.
Example 2: Event Merchandise
A company needs 100 custom t-shirts for an event.
- Solution: DTF printing is cost-effective and produces high-quality textile designs.
Example 3: Outdoor Signage
A business requires weather-resistant outdoor banners.
- Solution: UV printing is the best choice for durable, large-format prints.
9. Challenges and Future Trends
Challenges:
- UV printing requires specialized equipment and skilled operators.
- DTF printing may have environmental concerns due to adhesive powders.
- UV DTF designs can be rigid, limiting their application on curved surfaces.
Future Trends:
- Advancements in ink technology to improve flexibility in UV printing.
- Eco-friendly materials and processes in DTF production.
- Innovations in UV DTF to enhance adaptability for diverse surfaces.
10.Conclusion
UV, DTF, and UV DTF printing technologies each offer unique benefits tailored to specific applications. By understanding their differences, businesses and creators can select the right method to achieve high-quality, cost-efficient results.
Whether you’re printing durable signage, vibrant apparel, or custom non-textile items, the key lies in aligning your project requirements with the strengths of each technology. Stay informed and leverage these innovations to elevate your creative and business endeavors.